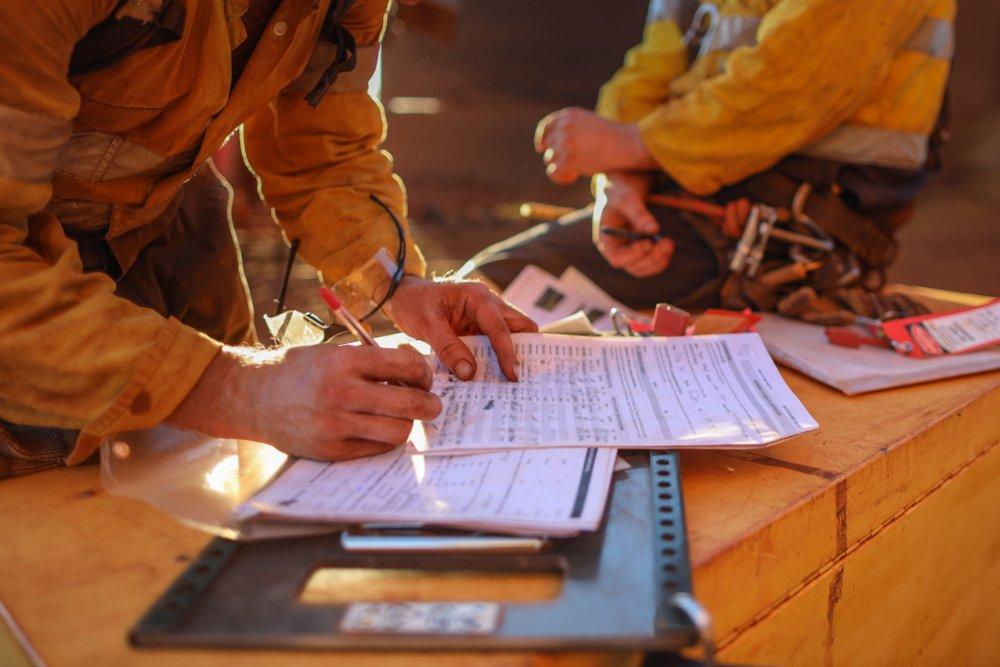
The global construction industry is expected to grow by eight trillion dollars by 2030. With this information, it’s reasonable to assume that the industry is cruising into the future with few to no barriers. That, unfortunately, is not the case.
Because of the industry’s growth, it’s easy to overlook some of its most serious concerns, such as a labor shortage, repeated project cost overruns, and a lack of construction productivity. In fact, yearly productivity growth in the sector has been only 1% over the last 20 years.
Lack of technological development
While various technologies are transforming the construction industry, the majority of them focus on how projects are designed rather than how they are completed. Indeed, many of the “tools” utilized in the field today are the same ones that have been used for the past 30 years – paper, pencils, and phone calls. Indeed, up to 40% of construction companies still utilize paper and pen on building sites!
This is an issue since these tools make the construction process more prone to errors. Throughout the project, daily reports, punch lists, and designs are regularly updated. However, the usage of pens and paper to track this information makes thorough communication difficult – if not impossible. Construction projects require hundreds, if not thousands, of hands on deck, and teams must adopt technology that will make the process run more smoothly.
Coordination constraints
Each construction project may include hundreds – or thousands – of workers united in various jobs with distinct objectives. General contractors, specialist contractors, suppliers, architects and designers, and project owners must all collaborate to formulate and implement a plan. While they are all working toward the same goal, they are working on different teams.
Obviously, achieving the required level of teamwork is easier said than done, especially when those participating are all using different technologies – or none at all. It is, however, necessary, because a lack of cooperation on construction projects leads to errors and wasted time.
Inefficient time management.
Thirty percent of a craftsperson’s time is spent on actual building. But where does the extra time go? The remaining 70% is spent on task preparation and gathering equipment and resources. A portion of that time is spent waiting to be told what to do next. According to a report, people waste up to 90 minutes per day merely “searching for items.” While planning is crucial, the main focus of time should be on construction. Otherwise, construction projects will be delayed and would incur large cost overruns.
Ineffective communication
Communication is necessary for success in almost any activity, but it is especially critical in construction. Every project has several moving pieces that might change on a regular basis. As previously said, paper and pen updates will not suffice. In reality, onsite misunderstanding and inaccurate data amount to $31 billion in reworking.
Lack of context around tasks
Craftspeople are frequently given work with little to no context. Simply said, they are instructed what to do but are not given the necessary information to accomplish a task efficiently. They are assigned tasks without any blueprints, images, or paperwork to help them completely comprehend what they should be doing and where they should be doing it.
This problem adds to the building industry’s already massive operational waste. Because of its productivity lag, the sector is currently wasting $1.6 trillion. Closing the gap between plans and duties will eliminate waste, helping the entire industry.